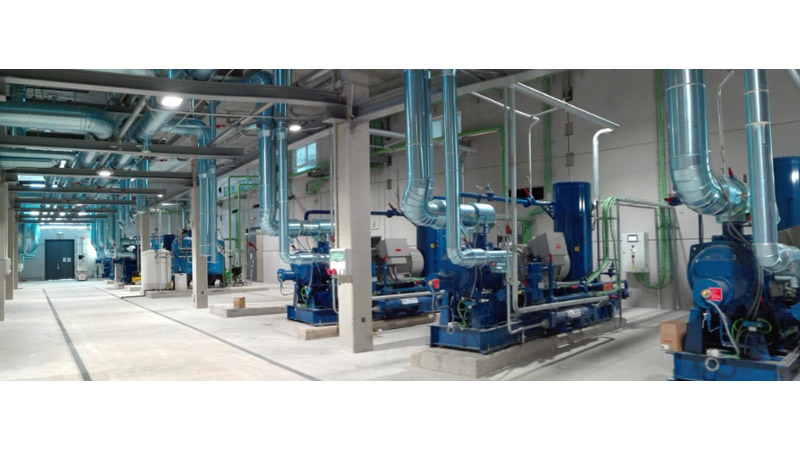
En un contexto económico globalizado y de máxima competencia, las empresas buscan de manera continua mejorar sus costes y de esta manera poder incrementar su competitividad. En el ámbito de la gestión energética, cada vez más empresas son conscientes del potencial de ahorro y de reducción de costes existente, no sólo a la hora de contratar su suministro energético sino también, a la hora de racionalizar y optimizar los consumos en sus procesos productivos.
La gestión energética es una herramienta de mejora de la competitividad y a su vez una oportunidad para reforzar la sostenibilidad de sus actividades productivas, reduciendo sus emisiones de CO2 y contribuyendo a la protección del medio ambiente.
Para dar respuesta a estas necesidades, en EDF Fenice Ibérica hemos desarrollado un modelo de Socio Energético Global, que ofrece un acompañamiento a las empresas, diseñando para cada cliente una oferta de servicios de eficiencia energética a medida, a partir de las mejores tecnologías disponibles adaptadas a sus necesidades y siguiendo el modelo de garantía de ahorros e inversiones autofinanciadas. Un modelo, que permite además a las empresas centrarse en sus actividades de core-business, confiando de esta manera la gestión energética a un especialista que tenga la capacidad de garantizar resultados y ahorros, así como la implementación de soluciones tecnológicas innovadoras, siempre apoyadas y respaldadas por un conocimiento experto y referenciado.
En este artículo, se presenta un caso de implantación real y de éxito del modelo descrito anteriormente, en una fábrica en el sector heladero, ICFC, quien tomó la decisión de llevar a cabo un proyecto de mejora de eficiencia energética o Plan General de Energía considerando la existencia de una potencia de eficiencia energética importante en la gestión de sus activos e instalaciones energéticas.
Eficiencia energética en fábrica del sector heladero
La industria en cuestión se encuentra ubicada en la Comunidad Valenciana. Es una industria dedicada al sector alimentario, más concretamente a la fabricación de helados. La fábrica data de la década de los 1960. La planta se abastece de gas, electricidad y agua. El gas es consumido en dos calderas pirotubulares para la generación de vapor saturado empleado fundamentalmente en procesos de pasterización y limpieza. Por su parte, los principales consumidores de electricidad son el frío (tanto para la fabricación como conservación de los helados) y el aire comprimido. En este caso también es especialmente relevante el consumo de agua de pozo, fundamentalmente porque es empleado en la condensación del refrigerante.
El consumo energético durante el año 2016 fue de aproximadamente 25,2 GWh anuales de electricidad, 13 GWh PCS de gas (11,8 GWh PCI) y 4 · 106 de m3 anuales de agua.
Medidas de ahorro energético implantadas
Las MAEs se centraron en los principales vectores energéticos y comprendieron:
- General: debido al crecimiento de la fábrica y las sucesivas ampliaciones respecto de su diseño original, existían múltiples salas técnicas en las que se encontraban dispersos los equipos energéticos (compresores de amoniaco, de aire, calderas, etc.) por toda la fábrica. Esta situación llenaba de conducciones la fábrica, que de otra forma serían innecesarias, con las consecuentes pérdidas energéticas. Además, implicaban que estos equipos estuviesen ocupando zonas en el interior de la fábrica de gran utilidad para situar nuevas líneas de producción. Es por ello que se decidió construir una nueva nave de “Servicios Energéticos”, en la que se localizasen los equipos de producción de frío y aire comprimido, así como las instalaciones eléctricas que les abastecen.
Asimismo, también se decidió migrar el actual sistema de seguimiento energético hacia otro nuevo sistema de gestión energética robusto, moderno y potente que permitiese un seguimiento real de las instalaciones principales, manteniendo parte de la instrumentación existente, pero instalando nueva instrumentación en las ubicaciones necesarias o donde el dispositivo no era adecuado.
- Frío industrial: la instalación de frío industrial existente presentaba varios problemas:
- Equipos antiguos, con baja eficiencia.
- Generación en varias salas independientes con recorridos sinuosos, lo que multiplicaba las pérdidas térmicas y la pérdida de carga, especialmente en las conducciones de frío de retorno.
- Falta de un control automatizado.
- Consumo elevado de agua, debido al sistema de condensación fundamentalmente.
- Ciclo frigorífico ineficiente.
Es por ello que se diseñó una instalación totalmente nueva, capaz de abastecer tanto a las líneas existentes como a las nuevas.
- La instalación está unificada en una sola sala que cuenta con compresores de tornillo de última tecnología equipados con regulación de velocidad, Vi variable, etc.
- También se ha instalado un moderno SCADA que gobierne de forma conjunta todos los equipos de forma que se maximice la eficiencia. Además, permitirá una racionalización de la explotación, liberando recursos a otras tareas.
- Adicionalmente se han instalado modernos condensadores evaporativos y control de condensación flotante para racionalizar el consumo de agua y maximizar la eficiencia. También cuentan con ventiladores con perfil para bajo nivel sonoro, como aconseja la conciencia ambiental.
- Por último, se ha diseñado un nuevo circuito frigorífico más eficiente en booster, con economizadores tipo abierto en todos los niveles, minimizando conducciones y pérdidas de carga, con enfriamiento de aceite por termosifón, motores eléctricos de alta eficiencia, aislamiento, purgador de incondensables y deshidratador, etc.
- Aire comprimido: de forma análoga al frío, en este caso también existían dos salas (una oil free y otra con compresores lubricados) equipadas con compresores antiguos (algunos de ellos alternativos) y poco eficientes. Es por ello que, en este caso, la modificación consistió en:
- Única sala para generación de aire comprimido
- Nuevos compresores de tornillo exentos de aceite para todos los usos. Uno de ellos está equipado con variador de frecuencia para adecuar la generación a la demanda
- Nuevo anillo de distribución que permite reducir las pérdidas de carga de las redes actuales
- Nuevos secadores de aire de mayor eficiencia.
- Instalación térmica: (prevista ejecución en 2017): en este caso las MAEs propuestas son:
- Instalación de economizador para recuperar el calor de los gases de combustión
- Recuperación del calor actualmente perdido en las purgas
- Reparación del sistema actual de purga continua por conductividad
- Mejora del aislamiento en la red de vapor
- Recuperación del calor del gas caliente del amoniaco (antes de la condensación) y del de la refrigeración de los compresores de frío para generación de agua caliente, con el consecuente ahorro de gas natural.
Tipo de contrato de gestión energética utilizado
Para ejecutar este proyecto EDF Fenice firmó un acuerdo con la empresa heladera como Socio Energético Global. Este tipo de acuerdo implica una colaboración total entre ESE y cliente industrial, pues incluye el O&M de los equipos energéticos por parte de personal de EDF Fenice; la consultoría, la inversión, el diseño, el suministro/construcción y la puesta en marcha por parte de EDF Fenice de proyectos de eficiencia energética y, finalmente, la remuneración de acuerdo a un Protocolo de Medida y Verificación de los ahorros consistente con el IPMVP, los ahorros son garantizados y compartidos.
En este acuerdo las instalaciones son monitorizadas, realizándose un informe mensual de seguimiento energético. En él se incluye el cálculo de los ahorros reales obtenidos cada mes, que serán compartidos. También se aconseja al cliente en temas de contratación energética. Además, el hecho de que los ahorros reales se compartan hace de EDF Fenice un socio autoincentivado en la búsqueda de nuevas MAEs que permitan mejorar la competitividad de nuestro socio industrial.
Reducción de consumos previsto
Ahorro energético:
- Electricidad: >3.500 MWhe/a, equivalente al 14% de la factura eléctrica
- Gas natural: ≈3.600 MWh PCS/a (>3.200 MWh PCI/a), equivalente al 27,6% de la factura de gas
- Agua de pozo: 3 · 106 m3/a de agua, correspondiente al 75% del consumo
- Toneladas de CO2 evitadas: ≈2.500 tCO2/a, equivalentes al 22% del total
Ahorro económico: 420.000 €/a, equivalentes al 14,8% de la factura energética.